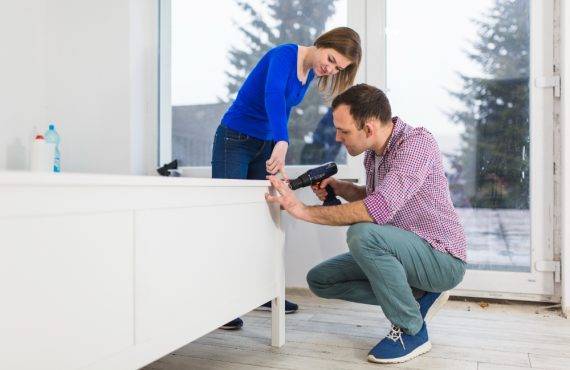
Introduction
The construction industry has evolved catalytically in recent years, moving beyond religious and linear methodologies and integrating innovative technologies and agile practices. In today’s time, modern methods of construction have bridged the shortcomings of traditional practices while paving the way for faster build times, streamlined project efficacies, sustainability, and reduced failure risks significantly. Whether it’s using laser layout techniques to prepare the 3D designs of the structures to be constructed or focusing on modular construction techniques to reduce traffic at the sites, several types of advanced practices are preferred nowadays.
Owing to this, we have prepared a detailed guide explaining modern versus traditional construction methods and the advantages and challenges encountered in both fields. With this, you will gain valuable insights into both MMC and traditional construction techniques and practices prevalent in the global industry to date and how they add value to a project.
What are the Modern Methods of Construction (MMC)?
Modern construction methods entail prefabrication of the building materials and aggregate components off the site and then transporting them to the destination for higher efficiency, faster development time, and enhanced sustainability. Some of the key examples of modern methods of construction have been described below.
- Off-site manufacturing: To reduce construction time and improve quality standards, different construction components are fabricated at factory levels and then transported to the site for final assembly.
- Modular construction: Large. Volumetric components are designed based on modular structures that can function independently to increase the structure’s scalability and design stability. It can significantly reduce the construction costs involved and shorten the project timeline.
- 3D printing: Another technique involved in MMC is fabricating intricate and complex construction elements using 3D printers to reduce material wastage and improve design quality.
- Panelized systems: Often integrated with traditional construction techniques, wall and floor panels are fabricated off-site and then assembled on the site to reduce construction time and facilitate the designing of intricate structures.
- Timber frame and light gauge construction: To increase assembly speed and implement precision and accuracy in structural dimensions and designs, timber and steel frames are often constructed in factories and then assembled at the site while maintaining modularity.
What is traditional construction?
Traditional construction follows a sequential format, where each step of the project needs to be completed mostly or wholly before the next step can commence. Brick-and-mortar practices are common, like on-site construction of the building materials, linearly constructing different structures of the building, and employing too many laborers at the site itself. To help you understand, we have given a few examples below.
- Brick and mortar construction: It involves creating different layers of bricks, one above the other, and joining them using a mortar paste to build entire structures, like pillars, walls, ceilings, and many more.
- Abode construction: Sun-dried clay bricks and tiles are used to construct the walls to impart thermal insulating properties within the building.
- On-site construction: All the building components, like timber frames, roofing shingles, window and door frames, and others, are constructed on-site and then assembled.
Comparison of MMC Vs Traditional Construction
Aspects | MMC | Traditional construction |
Construction speed | The total time taken for construction can be reduced by 30% marginally. | It takes lot of time to complete the construction due to sequential actions and on-site fabrication. |
Quality control | Off-site construction enhances quality and ensures consistency, thereby minimizing defects. | Quality assurance depends on the skills of the labor force, material quality used, environmental factors, and project planning. |
Costing | With a reduced labor force, off-site construction, and innovative techniques, MMC is highly cost-efficient. | The costs involved with a traditional construction project are quite high and comprise several additional overheads. |
Design flexibility | MMC is best suited for residential and commercial buildings where repetitive designs will be used. However, it’s not suitable for projects requiring customization. | Traditional construction offers excellent flexibility in customizing the designs and including intricate patterns and accommodating higher complexity. |
With this comparison, you now have clarity about modern methods of construction VS traditional techniques and the key aspects setting them apart. Hence, deciding the right approach based on your project scope and other external variables will become easier and less conflicting.
Advantages of Modern Methods of Construction
- As most building components are prefabricated at factory levels and then assembled on the construction site, project efficiency is improved by several notches, and delays due to unexpected weather conditions are minimized.
- Prefabrication speeds up the construction of building components, making MMC suitable for projects with a tighter timeline.
- One of the major advantages of modern methods of construction is optimal quality assurance and consistent designs of the prefabricated building elements due to the use of advanced technologies.
- In terms of cost, MMC is far more efficient since it can reduce financial budgets by 30%.
Advantages of traditional construction
- Traditional construction creates singularity and linearity in the projects, allowing builders and contractors to proceed chronologically.
- It can facilitate teamwork since everyone needs to work collaboratively to generate higher outputs.
- One of the major benefits of traditional construction is that it accommodates higher customization levels and complicated designs.
- Transparency is maintained from the beginning to the end of the project as all the actions and tasks are conducted on-site under proper supervision and guidance.
Challenges of Modern Methods of Construction
- MMC doesn’t offer flexibility in building custom structures with higher complexity levels.
- The upfront investment needed will be quite high to acquire the prefabricated materials.
- It involves enormous risks for assembling the components on-site.
Challenges of traditional construction
- The overall time taken to complete a traditional construction project is quite high.
- Delays can be introduced due to unpredictable weather conditions.
- Costings are way higher due to the involvement of on-site fabrication and large-scale labour employment.
Conclusion:
Modern methods of construction (MMC) and traditional construction approaches each have their own advantages, depending on the project’s goals and requirements. While MMC emphasizes speed, sustainability, and innovation, traditional methods focus on craftsmanship and time-tested reliability. Choosing the right method can significantly impact your project’s efficiency and quality.
Propchk offers expert home inspection services to ensure the quality and safety of your construction project, whether it’s built using modern or traditional methods. With Propchk, you can confidently validate structural integrity and compliance for a durable and reliable property.
FAQs:
Yes, MMC can be easily used for residential projects where multiple building components with the same design and structure are required.
With MMC, most building components are prefabricated at the factory level, which further enhances sustainability and reduces material wastage.
Traditional construction is still prevalent in the industry because it facilitates customization, establishes transparency, and allows proper quality control through diligent supervision.
MMC structures are durable enough but when compared to traditional buildings, the durability coefficient is somewhat low.