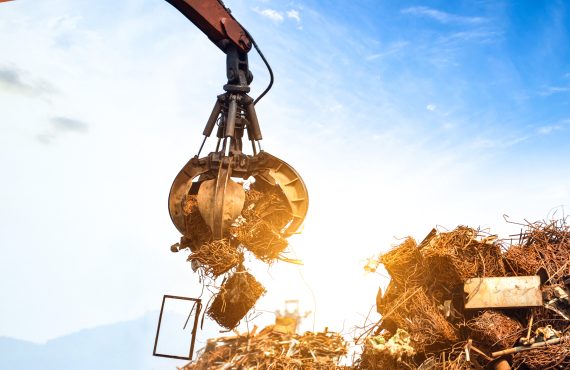
Introduction
Once the construction is completed, most project managers conduct a thorough check of the existence of any incomplete work, issues in the build, or other types of problems towards the end of the process, usually before the final handover to the client. This is what we call snagging in construction, a necessary step that ensures quality in craftsmanship and increases the chances of passing different types of inspection routines in one go. Snag checks and documentation contribute a lot in terms of meeting stringent industry standards and maintaining the overall construction and build quality at optimal levels. With this being said, we have prepared a detailed guide that you should know about snagging, including its benefits, the steps involved, the tools and techniques used, and the best tips to carry out the process.
What is snagging?
Although quality checks are ensured during the entire construction phase of any property, unwanted issues and minute defects may arise. If these are not controlled and fixed on time, there will be several interim issues with the handover process. Besides, it can also raise questions on the quality of the craftsmanship and the compliance of the construction process followed. That’s where snagging in construction comes into the picture! It can be defined as a detailed inspection process that allows contractors and project managers to deal with:
- Flaws that soon start to emerge with time, like paint blisters, cracks in the wall plasters, and swelling and warping in wooden floors.
- Issues arise in the construction due to poor craftsmanship.
- Project aspects that were missed or skipped during construction.
- Issues with material installation, quality, and improper design.
- Any latency in the issues mentioned above could cause severe problems later on.
Snagging is not the same as structural inspection. While the former is more focused on finding cosmetic defects and gaps in the final construction and the initial design, the latter is inclined towards checking structural integrity and stability.
Importance of snagging
Following are the benefits of snagging in construction that should be known beforehand.
- It helps identify minor defects, poor craftsmanship, and inconsistencies in the designs.
- Ensures the construction process meets client expectations and stringent compliance standards.
- Allows clients to confirm work quality before the final payment.
- Reduces the costs necessary to resolve these issues after handover due to latency.
- Verifies that all the installations, like fixtures, windows, and doors, have been done properly.
- Demonstrates the company’s commitment towards delivering optimal client satisfaction.
- Prevents any unnecessary delays in the final handover.
The snagging process in construction
Below, we have briefly explained the snagging process in construction.
Pre-handover inspection
The property is inspected to find snagging issues in major areas, such as paintings, plastered walls, fixtures and wiring, doors and windows, and more. It is primarily carried out once the construction is over, but the handover has yet to be done.
Creating a snag list
The issues and gaps found during the pre-handover inspection are adequately documented and are known as a snag list. It serves as a checklist for constructors and builders to fix the issues later on and prioritize the matters properly.
Reporting and rectification
The snag list is then reported so that proper measures can be implemented for further rectification. For instance, if there are cracks in the wall plaster, those are removed, and a fresh plaster layer is applied to resolve the issue. Similarly, any problem with material quality is handled thoroughly through rework.
Final inspection
After the rectification process is complete, a final inspection will be conducted to verify that all the issues and inconsistencies mentioned in the snag list have been addressed properly.
Tools and techniques for snagging
To ensure optimal quality in the snagging process in construction, a combination of multifarious tools and techniques are used, like:
Tools used for snagging
- Inspection tools like measuring tapes are used to check the dimensions and spirit levels to ensure the alignment of walls and laser level for precise levelling checks.
- Lighting tools like portable work lights and flashlights to detect the issues in poorly lit areas.
- Coloured tapes, stickers, and marker pens highlight the areas that have underlying issues or inconsistencies.
- Digital tools like snapping apps are used for documentation and annotation, and cameras are used for photographic proof.
- A few specialized tools are also used, like a moisture meter to check for dampness, a voltage tester to check the electrical wirings and outlets, and a thermal imaging camera to verify heat loss and insulation levels.
Snagging techniques
- Systematic walkthrough: Chronological inspection of rooms, floors, and other areas without missing a corner.
- Functional testing: Running taps to check water flow, testing switches and sockets, checking smooth operations of windows and doors, and many more.
- Referencing standards: Comparison of the final work with the design standards and specifications, building codes, and the initial contract agreements.
- Surface inspection: Conducted to find any cosmetic defects like swelling and warping, chipped paints, and cracks in plastered walls.
Snagging problems for new builds
- One of the significant snagging problems with new builds is cosmetic and finishing issues, like cracked plasterwork, poorly applied paint layers, misalignments in skirting boards, and squeaky flooring.
- Issues in the bathroom and plumbing are also included in the snagging list, like low water pressure, inadequate waterproofing, and leaking sinks.
- Electrical issues like improper location of the outlets, poor insulation, exposed wires, faulty switches, and flickering lights.
Avoiding snags in the first place
Importance of hiring experienced contractors
One of the best ways to avoid snagging in construction is to hire experienced contractors at the first place who are well aware of the industry standards and building codes.
Regular site inspections during the construction process
Proper site inspections should be conducted regularly during the construction process to check for material quality, design consistency, and craftsmanship quality.
Straightforward contracts with detailed quality standards
The construction contract must be properly outlined with detailed standards regarding the expected craftsmanship quality, and these standards should be followed throughout the build process.
Use of high-quality materials and skilled labour
Materials should be checked for quality and shouldn’t be compromised. Also, it’s imperative to hire skilled labour who knows how to use the materials and adhere to the construction designs.
Conclusion
Here, we have explained everything you need to know about snagging in construction, from the major areas that could be affected to the tools and techniques used for the inspection. The illustration of its importance shows that if skipped, it can lead to severe consequences, like delayed handover, costly repairs, and more.
FAQ:
No, snagging is conducted by the constructors and builders before the final handover.
The snagging process can take from a few days to several weeks, depending on the snag list prepared and the extent of rectification required.
Professional snagging services are expensive but worth the investment since they help you identify issues and inconsistencies properly and in detail.
Once the rectification is complete, a final inspection needs to be conducted, and the results should be verified against the snag list without skipping any point.